Investigating formability behavior of friction stir-welded high-strength shipbuilding steel using experimental, finite element, and artificial neural network methods
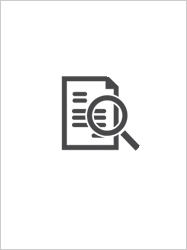
Göster/ Aç
Erişim
info:eu-repo/semantics/closedAccessTarih
2024Yazar
Sekban, Dursun MuratYaylacı, Ecren Uzun
Özdemir, Mehmet Emin
Yaylacı, Murat
Tounsi, Abdelouahed
Üst veri
Tüm öğe kaydını gösterKünye
Sekban, D.M., Yaylacı, E:U., Özdemir, M.E., Yaylacı, M. & Tounsi, A. (2024). Investigating Formability Behavior of Friction Stir-Welded High-Strength Shipbuilding Steel using Experimental, Finite Element, and Artificial Neural Network Methods. Journal of Materials Engineering and Performance, 34(6), 4942-4950. https://doi.org/10.1007/s11665-024-09501-8Özet
Steels are preferred in the building of commercial ships because they can be easily welded and supplied. Although it varies according to the parts of the ships, it is known that high-strength steels are preferred especially in bulb and side coatings where relatively high strength is desired during the building process. In the process of welding these steels, mostly gas and submerged arc welding are used. On the other hand, studies continue for the use of the new generation friction stir welding (FSW), which is known to have many advantages over existing welding methods, in the shipbuilding process. The formability of the welded plates in the construction process of the ships is extremely important to give the necessary form to the ship. On the other hand, post-weld formability properties are of great importance for determining the strength and elongation values in wave crests and wave troughs to which ships are exposed during navigation. In this context, in this study, relatively high-strength AH32 shipbuilding steel was joined with FSW and the formability behavior of the welded region was investigated comparatively by experimental, finite element analysis and artificial neural network methods. As a result of the studies, it was determined that the strength values in the weld zone of the steel joined by FSW increased compared to the pre-weld and the formability behavior did not deteriorate. In addition, it was determined that the results of finite element analysis and artificial neural networks were extremely consistent with the experimental data, and it was determined that the models created in the study would give close results to the real results even without experimental studies.